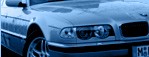


BMW 7er, Modell E32 |
 |
|
Varianten |
|
Detail-Infos |
|
Interaktiv |
|

- Anzeige -
|
 |

|
|
|

|
 |
|
20.06.2012, 08:19
|
#241
|
12-Zylinder Pilot
Registriert seit: 31.03.2011
Ort: München
Fahrzeug: E32 750i, Prod. 10.03.1989 / E65 760i Individual, Prod. 26.04.2004 / Indian Chieftain, 2016
|
Zitat:
Zitat von Asrael
Servus,
nachdem ich mit dem Chip in meinem 735 sehr zufrieden bin, jetzt noch einen 750 habe, wollte ich fragen ob es für den 750 auch einen Chip gibt und wie der sich "bemerkbar" macht.
|
Die Chips bieten eine etwas progressivere Gaspedallinie, er hat mehr Druck unten raus, bei EML-Chip ist er offen, bin meinen aber noch nie ausgefahren. Schönes Kaltstartverhalten (kurzzeitig erhöhte Leerlaufdrehzahl), läuft butterweich. Lohnt!
__________________
"Aerodynamik ist nur etwas für Leute, die keine Motoren bauen können." (Enzo Ferrari)
|
|
|
03.07.2012, 12:07
|
#242
|
Shogun
Registriert seit: 19.07.2002
Ort: Joso
Fahrzeug: E32 750iL 11/88
|
Reset Getriebesteuergeraet
Gerade einen Hinweis zu Getriebesteuergeraeten gelesen. Ich zitiere:
Gilt fuer EGS als auch AGS.
Steuergerät zurücksetzen:
Zündung auf Stufe 2, 3x Gaspedal durchdrücken (quasi den Kickdownschalter betätigen), Zündung wieder aus.
Was hat man, EGS oder AGS?
Erkennbar an deinem Kombiinstrument/Programmwahlschalter. Wenn du noch das separat wählbare Winterprogramm hast, dann hast du EGS.
Die Steuergeräte, ob nun AGS oder EGS, sind gleich. Der einzige Unterschied ist der Chip der da draufgesteckt ist.
Zitat Ende
Es ging in diesem Fall um die Frage wann die WÜK schließen soll.
|
|
|
19.08.2012, 08:26
|
#243
|
Neues Mitglied
Registriert seit: 03.01.2012
Ort:
Fahrzeug: E32-740i (11.92)
|
I am running the chip for E32 M60 and this is my observations after about 2000 km of driving:
-Engine has better low and midrange part throttle torque.
-Gas milage is improved by around 6%.
I am very happy about the results as this is what I was loking for!
What octane fuel is recommended for this chip? I am currently running 98 octane for saftey, since I dont have a possibility to scan for detonation.
Have anyone comfirmed its safe to use this chip with 95 octane fuel?
Sorry I have to write in English, my writing skills in German are not so good.
|
|
|
19.08.2012, 09:27
|
#244
|
Shogun
Registriert seit: 19.07.2002
Ort: Joso
Fahrzeug: E32 750iL 11/88
|
thanks for the good results.
As for fuel, your car has knock sensors. Here the details of the DME M3.3:
DESCRIPTION OF THE DME 3.3 SYSTEM USED ON E32 V8’s
· Cylinder-individual fuel injection with correction facility "CIFI"
· Direct-fire injection system (Coil-Over-Plug with 8 output stages)
· Parallel ignition stage mode in the case of cylinder reference failure
· Ignition circuit monitoring (primary and secondary circuits)
· Idle control with two-winding actuator (ZWD)
· Cylinder-selective, adaptive knock control with 4 sensors
· Stereo lambda control
· Load setting via hot-film air mass meter HFM
· Incremental system for engine speed and reference mark signal
· Cylinder reference by inductive pulse generator on camshaft gear
· Engine torque limitation on automatic transmission vehicles
· Engine speed limitation
· Speed limitation by V-signal
· Electrical fuel pump activation (EKP) with safety lockout function at speed zero
· Characteristic map-controlled tank ventilation
· ASC engine intervention (Automatic Stability Control)
· Cylinder charge intervention with ASC throttle actuator
· Drive-away protection via anti-theft system (DWA)
· Characteristic map programming
· Idle CO adjustment-Secondary air pump control for US models
· Interface to AGS via CAN (Controller Area Network) data bus
· Ignition timing (angle) intervention by adaptive transmission control (AGS)
· Self-diagnosis and emergency operation characteristics
Fuel injection control of DME M3.3
When the ignition is switched on, initially fuel is briefly injected once at all cylinders. Once the start procedure has been initiated, fuel is then injected cylinder-selective 1 x per working cycle (2 crankshaft revolutions).
The injection timing (ti) is derived from the programmed basic start injection quantity and the correction variables from the input signals for coolant and intake air temperature. Cylinder activation is based on the position of the reference mark signal. After few engine revolutions (dependent on the position of the camshaft and the start speed) the DME control unit receives the signal from the camshaft position sensor. Double ignition (one ignition during each crankshaft revolution) takes place until the camshaft position is
detected. It can now be seen whether the ignition allocation needs correcting. The double ignition function is retained if the camshaft position sensor signal is not detected with the engine running. In this case, it is not guaranteed that the ignition timing takes place within the working cycle.
Acceleration enrichment is always activated when the load requirement of the driver (throttle potentiometer signal) and the engine speed render this necessary. Intermediate injection takes place at the cylinders that have already completed their injection time cycle. For the subsequent cylinders, the normal injection timing (ti) is extended for fuel enrichment. The DME M3.3 features cylinder-individual fuel injection CIFI. The term CIFI refers to individual activation of each cylinder. The system ensures that fuel injection of each cylinder is completed before the inlet valves opens. An optimum fuel-air mixture and thus improved combustion with low fuel consumption is achieved in this way.
The output stage of each cylinder can be switched off individually if there is a fault in the ignition or fuel injection system. These faults are then also stored in the defect code memory.
Ignition system with static high-tension distribution
A separate output stage-controlled ignition coil which transfers the high tension (up to 32 kV) via the spark plug connector is provided for each cylinder. In this way, changes to the ignition timing can be controlled
rapidly and independently. The effective range for ignition timing control is increased because there are no rotating parts. The camshaft sensor is used to ensure the correct firing order is maintained. Based on the engine speed and load signals, the DME control unit determines the ignition angle (ignition
timing), which is output via the ignition output stages. This function also considers other input signals such as the engine temperature, intake air temperature, throttle position, knock control signals and adaptive
transmission control signals. In the event of failure of the cylinder reference sensor (camshaft sensor), the system switches over to parallel ignition, i.e. the ignition coils of the individual cylinders are controlled with fixed ignition timing values during each crankshaft revolution.
Ignition circuit monitoring
The task of ignition circuit monitoring is to detect misfiring cylinder-selectively (self-diagnosis) and to prevent damage to the catalytic converter. Exhaust gas emissions cannot deteriorate because fuel injection
is cut out for the cylinder concerned. The secondary circuit-monitoring feature operates with a "shunt" (resistor in the common secondary ground
line of the 8 ignition coils). The voltage progression at the shunt is transferred to the control unit for each cylinder. If after successful ignition (cylinder-selective primary circuit monitoring ok.) the threshold voltage for
misfiring detection (5V) is not reached, the defect code is set, the defect lamp activated (US models only) and the relevant injection output stage is switched off.
Idle control
A new no-wear two-winding actuator is installed in the M60 engine as the idle actuator. The rotary slide valve in the idle actuator should only be tested by activation in conjunction with a tester or by shaking. The rotary valve must not be moved with the finger or with the aid of a tool such as a screwdriver for instance. Perfect operation could then no longer be guarantied. The idle actuator performs several tasks and is therefore an important component part in the intake air circuit of the engine. Small quantities of leakage air that occurs, for instance, at leaking gaiters/bottles or varying gap of the throttle can be compensated by means of the idle actuator. During the engine thrust phase, the actuator opens completely and then closes shortly before reaching the idle speed. This prevents a high intake pipe vacuum and blue smoke (oil vapour intake via valve stem
seals). During engine start, the idle actuator releases an opening cross section that is above the idle speed. This improves the engine starting characteristics. The idle actuator features an emergency operationopening
gap that ensures certain emergency operation characteristics in the event of power failure. On vehicles equipped with ASC or ASC+T, the engine drag torque is controlled by the idle actuator (MSR function). The idle actuator opens if there is a risk that the drive wheels can come to a standstill. As a result, the engine speed is increased and the engine drag torque reduced.
Knock control
Tasks of the knock control system
Operation of an engine with knocking combustion over a prolonged period can lead to serious damage.
Knocking tendency is increased by:
-increased compression ratio
-high cylinder charge
-poor fuel quality (RON/MON)
-high intake air and engine temperatures
The compression ratio can also reach excessively high values due to deposits or production-related scatter.
On engines without knock-control, these unfavourable influences must be taken into consideration in the ignition design by providing a safety distance to the knock limit. However, this results in unavoidable losses in efficiency in the upper load range.
The knock control can prevent knocking engine operation. For this purpose, it retards the ignition timing of the cylinder(s) concerned (cylinder-selective) as far as necessary only when there is an actual danger of engine knocking. In this way, the ignition characteristic map can be laid out to combustion-optimum values without having to consider the knock limit. A safety distance is no longer necessary. The knock control system carries out all knock-related corrections to the ignition timing and enables perfect operation with regular grade fuel (minimum RON 91).
The knock control provides:
-protection against knocking damage also under unfavourable conditions
-High efficiency due to optimum utilisation of the fuel quality and consideration of the relevant engine status
-logistics advantages with regards to fuel availability
-lower consumption and higher torque over the entire upper load range (corresponding to the fuel quality used).
Design of knock control system
The M60 is equipped with a cylinder-selective, adaptive knock control system. Four knock sensors detect knocking combustion. The sensor signals are evaluated in the DME control unit. The knock sensor is a piezoelectric structure-borne noise microphone. It picks up the structure-borne noise and converts it into voltage signals.
Function of the knock control system
If knocking occurs, the ignition is retarded for a certain number of working cycles and then gradually approaches the original value. Retardation can be controlled individually for each cylinder (cylinder - selective). Only the cylinder that is actually knocking is therefore influenced. If the knock sensor fails, a defect code is stored in the defect code memory of the DME control unit. In this case, a constant retardation setting of the ignition timing protects the engine.
Installation location/conditions
The 4 knock sensors are secured by means of 8 mm screws on the water jacket of the engine block between the 2 rows of the cylinders. They are arranged such that one sensor monitors each of the 2 adjacent cylinders. Only screw locking compound may be used to lock the screws, Washers, spring washers or serrated lock washers must under no circumstances be used.
Self-diagnosis and emergency operation of the knock control system
Self-diagnosis of the knock control system includes following checks:
Check for sensor signal interference/line break, plug connector defective etc.
Self-test of entire evaluation circuit
Check of the basic engine noise level recorded by the knock sensors
The knock control system is switched off if a fault is found during the course of one of these checks. The emergency program adopts the task of controlling the ignition timing. At the same time, a defect code is
stored in the defect code memory. The emergency program ensures damage-free operation as of minimum RON 91. It is dependent on the load, speed and temperature of the engine. The diagnosis procedure cannot detect whether the plug connectors of the sensors have been interchanged. The engine can be damaged if the sensors are interchanged. Particular care must be taken during service work to ensure that the sensors are connected correctly (see repair instructions).
Stereo lambda control on models with catalytic converter
In order to maintain optimum efficiency of the catalytic converters, the system endeavours to provide the ideal air-fuel mixture ratio (Lambda = 1) for combustion. The system features 2 heated oxygen sensors (1 for each row of cylinders with relevant exhaust gas line = stereo lambda control) that measure the residual oxygen in the exhaust gas and send corresponding voltage values to the control unit. Here, if necessary, the mixture composition is corrected accordingly in that the injection timing varies. In the event of the oxygen sensor failing, the DME control unit takes over control with a fixed programmed substitute value (0.45V). Since the oxygen sensors require a temperature of approx. 300 degrees Centigrade in order to operate efficiently, voltage is supplied to the heating resistors in the oxygen sensors via a relay. The DME control unit controls relay activation.
Hot-film air mass meter
A heated area of the hot-film sensor in the flow of intake air is controlled to a constant over temperature of 180 degree C. with respect to the intake air. The intake air flowing past cools the heated surface and thus varies its resistance. The heating current which is necessary in order to maintain the constant temperature is the measurement variable for the air mass drawn in. The DME control unit uses this variable to calculate the injection timing.
Important advantages
-changes in air pressure (air density) are recorded
-temperature influences are compensated
-no moving parts
-large measuring range
-low pressure drop in intake pipe due to low air resistance, thus improved efficiency of the engine.
The hot-film air mass meter renders unnecessary clear burning of the sensor after the engine has been shutdown. Any dirt deposits on the surface do not influence the sensor signals directly since the protective film cleans itself due to the constant over-temperature.
Tank ventilation on models with catalytic converters
The ventilation line of the fuel tank is connected to an activated carbon filter (carbon canister), in which the fuel vapours produced in the tank are collected. The activated carbon filter is connected by way of a further
line to the air collector. A tank ventilation valve is integrated in this line. If the tank ventilation valve is opened, the vacuum in the air collector draws in fresh air via the activated carbon filter. The fresh air flushes out the fuel collected in the filter and feeds it to the engine for combustion. Since the additionally supplied mixture influences combustion to a considerable extent, the tank ventilation valve is made up of a non-return valve and an electrically operated valve. When no power is applied, the non-return valve keeps the tank ventilation valve closed. The non-return valve prevents fuel collecting in the air collector when the vehicle is parked. The non-return valve opens as the vacuum in the air collector increases. Electrical activation (pulse cycle) is dependent on engine speed and load. A ventilation cycle (purge phase) begins as soon as the lambda control is active. After a cycle has been completed, the valve closes for approx. 1 minute (rest phase).
CO-correction on models without catalytic converter
Correction can be carried out by a compensating value in the DME control unit. This CO adjustment can only be implemented by way of corresponding diagnosis program.
Adaptations
The fuel-air mixture formed in the intake tract requires a certain period until it reaches the oxygen sensor in the form of exhaust gas. This time decreases as load and engine speed increase. For this reason, the response time of the emission (lambda) control system is also dependent on load and engine speed. Fuel/air mixture deviations detected by the oxygen sensor result in adaptation values (learned correction values) being stored. By way of the adaptations, the injection can be brought close to the nominal value in
advance. A reduction in the response time is achieved in this way. For instance, if the basic injection values of the DME characteristic map were too low during idling or in order to maintain the ideal fuel-air mixture, the emission (lambda) control system would have to constantly increase the injection timing. In this case, an adaptation value is learnt which corrects the basic injection value. The emission (lambda) control then only needs to undertake the fine adjustments. Following adaptations are performed during engine operation:
Tank ventilation adaptation
When the tank ventilation valve is open, an additional combustible mixture is supplied from the activated carbon filter to the engine. The shift in the air-fuel ratio detected by the oxygen sensor is almost completely compensated by means of the tank ventilation adaptation value.
Idle air adaptation
The task of idle air adaptation is carried out by the idle air actuator. Based on the air volume it ensures a constant idle speed.
Idle mixture adaptation
If idling is detected based on the throttle position during the rest phase of the tank ventilation system, idle mixture adaptation takes place at certain intervals.
Partial load mixture adaptation
Also in the partial load range. Mixture adaptation takes place at certain intervals. The determined adaptation value is taken into consideration in all partial load ranges.
Intake air temperature sensor (NTC-I)
The intake air temperature sensor is screwed into the air collector. A precision NTC resistor is used to convert the 'temperature' into a measurement value 'resistance' which can be evaluated electrically by the
DME control unit. The intake air temperature sensor is not required for correction of the injection timing since the intake air temperature is taken into consideration automatically during air mass measurement. The intake air
temperature sensor (NTC-I) is required during the start procedure in conjunction with the coolant temperature sensor (NTC-II). The resistance values of both sensors supply exact information for calculating the injection timing. In this way, hot start problems are avoided. The air column in the air mass meter can vibrate during the start procedure. As a result, the output value of the air mass meter cannot be used as a correct value for injection timing. For this reason, the temperature sensors are used as measurement variables during the start procedure up to a freely programmable engine speed threshold.
Speed signal
The input of the driving speed signal (V-signal) is required in the DME control unit for several functions. It serves the purpose of maintaining the programmed maximum speed. Once this speed is reached, the individual ignition and injection signals are masked out. This ensures smooth shutdown.
On vehicles with the air conditioning switched on, compressor activation is interrupted up to a driving speed of 13 kph when accelerating under full load.
The idle speed is controlled at a driving speed signal >0 kph, i.e. the idle speed has a fixed value which is normally just above the engine speed when the vehicle is stationary. The idle speed is controlled if the driving speed is 0 kph. However, it is still corrected by the air conditioning system signal, the drive stage information on automatic vehicles and the light switch input.
The incoming V-signal in the DME control unit is made available via the CAN interface to the adaptive transmission control unit (AGS).
ASC interface (Automatic Stability Control)
A choke with actuator motor and an ADS control unit (independent throttle control) are installed on vehicles equipped with ASC.
Functions
ASC/MSR control (engine drag torque control) is realised by way of following functions:
-the DME control unit processes the incoming information from the ABS-/ASC control unit. It performs the tasks of blanking out the ignition (ZA) and interrupting fuel injection and drives the idle actuator as well as the control motor of the automatic throttle actuator in conjunction with the ADS control unit.
The idle actuator opens specifically when the engine drag torque control is activated. It receives its pulse width-modulated signal directly from the DME control unit. The ADS control unit activates the throttle actuator motor. It is linked by means of a cable assembly with the choke and reduces the engine speed as required. The choke is an additional throttle which is connected upstream of the central throttle. It is opened under spring load (normal status) and is closed by the throttle actuator during ASC control.
ABS/ASC interface
The following ACD-DME interface is required for activation of the necessary ASC functions within the DME M3.3 or for evaluation of the engine speed:
Description..... DME control unit.... ABS/ASC control unit
Ignition timing...... unit Pin 82............ Pin77
Ignition mask out..... Pin83............... Pin81
Idle speed increase...Pin62.............. Pin18
Engine speed signal... Pin20............. Pin47
Actual throttle value.. Pin11............. Pin20
Based on the extend of slip, the DME control unit receives information from the ABS/ASC control unit. The ABS/ASC control unit determines the control or control combinations to be carried out by the DME control unit. The maximum time the signal inputs are applied at the interfaces is less than 2 seconds. If one or several inputs are applied longer than 2 seconds, a defect code is stored in the defect code memory and the ASC is deactivated.
Masking out ignition and fuel injection (ZA):
The ZA function for DME M3.3 corresponds to the function as already implemented within the DME 1.1, M1.2 and 1.7 for M30 and M70 engines.
If the idle speed increase (anti-stall function) and ignition mask out are activated simultaneously, in addition to the throttle adjustment, the ignition is masked out and fuel injection interrupted. Ignition mask-out takes place for a maximum 2 seconds.
Ignition timing adjustment (ZWV):
In the same way as the function in DME M1.7, the ignition timing is retarded when ASC is activated.
Idle speed increase (anti-stall)(LDA):
Based on the opening of the idle actuator, the MSR function (engine drag torque control) is implemented via the DME when the vehicle is coasting. When the signal is applied, the idle actuator is opened further in order to reduce the drag torque of the engine and to prevent the rear wheels skidding. In addition, the DME cancels the deceleration fuel cutout so that the engine does not stall. When a vehicle with ASC reaches the control range, the ASC/ABS control unit sends corresponding signals to the DME control unit (see ASC functions). In addition to ignition timing adjustment or ignition mask-out of the DME control unit, the ADS control unit can close the choke in order to reduce the engine speed. In order to be able to decide the extent of the necessary choke adjustment, the ADS control unit receives the
actual throttle value of the DME throttle. With the aid of the ADS actuator motor, if necessary, the throttle may be adjusted against the wishes of the driver (accelerator pedal).
Antitheft system (DWA)
The vehicle is protected against theft by the DWA input. The input is active when high signal is applied. The antitheft system is active up to a certain engine speed threshold. The speed sensing function prevents the vehicle being stopped in the event of a defect in the multi-information display MID or in the antitheft system (DWA). Below this speed threshold, the antitheft function is triggered if high signal is applied. In this case, the DME M3.3 prevents the engine from being started. It is not possible to push start the engine when in this status.
Secondary air system (US cars only):
An air pump is used to subsequently treat the exhaust gas. This vane pump is driven mechanically by means of a V-belt. The support bracket for the air pump is mounted on the A/C compressor. Air is injected via hoses and lines into the longitudinal duct in the cylinder head and from here into the output ports. 2 non-return valves and a shut-off valve prevent exhaust gas flowing back to the air pump. The pneumatically operated shut-off valve is driven by an electric switchover valve. The system is switched by means of a magnetic clutch as required.
The CAN bus (controller area network) is a serial bus system, in which all connected stations are equally entitled, i.e. each control unit can both send as well as receive. In other words, the connected control units can 'communicate' and exchange information via the lines. Due to the linear structure of the network, the bus system is fully available for all other stations in the event of one failing. The connection consists of 2 data links (CAN_L and CAN_H) that are interference-protected by means of shielding (CAN_S). At present, the AGS and DME control units are interconnected with this system. Linking in of further controls will follow. The connected control units must have the same CAN status. The CAN status can be checked via the diagnosis interface. The CAN status (bus index) is specified on the identification of the relevant control unit connected to the CAN bus.
Following information can be interchanged via CAN with the adaptive electronic transmission controls AGS:
Terminal 15 (ignition ON)
Engine speed
Coolant temperature
Engine load signal
Vehicle speed
Throttle angle
A/C compressor
Engine torque reduction by ignition timing adjustment
Torque converter clutch opened or closed
Selected drive program
Selector lever
Current drive stage
Deceleration fuel cut-out active or not active.
|
|
|
23.08.2012, 00:45
|
#245
|
Erfahrenes Mitglied
Registriert seit: 08.11.2009
Ort: HATTEN
Fahrzeug: 740IA E38 1994
|
Zitat:
Zitat von Stiefelknecht
Hi Captain,
mit dem ASC+T Problem waren wir zu zweit 
Kann aber vielleicht auch dran liegen das wir eben Hypochonder sind was den 7er anbelangt 
Ich hab den Chip mittlerweile wieder drin und hab mich an das Problemchen gewöhnt  Das Fahrgefühl mit dem Chip übertrumpft eben diese Macke.
Zum EGS,
auch da sind wir zu zweit was den Wiederausbau anbelangt.
Wir hörten einfach bei starkem beschleunigen von unten raus die Pumpe singen (hört sich jedenfalls so an), das war uns zu heiß, daher back to original.
Wenn du willst kannste ja meinen Chip haben zum ausprobieren
MfG
Chris
|
kleine idee
genau diese fehler meldung hab ich schon gesehen mit ein bmw automatikgetriebe (bei X5) und da war viel zu wenig oel ins getriebe, und dann das kardanwellegeschwindischkeit hat nicht mehr mit motorumdrehung gestimmt, und dein geräusch mit wenig öel könnte stimmen mit getriebechip (baut mehr druck und braucht mehr oel)
habe nicht alles 100% gelesen, aber hast du überhaupt getriebeöel und filter geweckselt?
wenn ja, hast du getriebe problem wo sich mit original chip nicht meldet
|
|
|
23.08.2012, 06:33
|
#246
|
Ärmstes Mitglied
Registriert seit: 28.08.2007
Ort: Elzach
Fahrzeug: 740i 12/92
|
Mit dem Getriebe ist alles im grünen Bereich
MfG
Chris
__________________
Nachrüstungen
original:
Vollleder / Standlüftung / M-Fahrwerk VA+HA / el. Heckrollo / Memory / AUC (mod. by Salzpuckel) / abl. Innenspiegel
andere Baureihen/sonstiges:
4-Kolben-Bremse vom 840er / BMW Professional RDS E36 / H&B Sportauspuff / Interface für Öltemp/Druck / Getriebetemp. / Innentemp. übers Kombi
|
|
|
23.08.2012, 06:45
|
#247
|
Erfahrenes Mitglied
Registriert seit: 08.11.2009
Ort: HATTEN
Fahrzeug: 740IA E38 1994
|
kommish... 
|
|
|
27.08.2012, 16:43
|
#248
|
Erfahrenes Mitglied
Registriert seit: 08.11.2009
Ort: HATTEN
Fahrzeug: 740IA E38 1994
|
Habe heute morgen die beiden chip bekommen! Lauft geil!!
|
|
|
02.09.2012, 20:13
|
#249
|
Erfahrenes Mitglied
Registriert seit: 08.11.2009
Ort: HATTEN
Fahrzeug: 740IA E38 1994
|
das verbrauch ist super!!!
eine strecke von 430km mit tempomat auf 120, damal war ich immer zwishen 10.5 und 10.7, und jet's 9.1! unglaublich!! 
|
|
|
23.10.2012, 05:04
|
#250
|
Shogun
Registriert seit: 19.07.2002
Ort: Joso
Fahrzeug: E32 750iL 11/88
|
@dimidu
danke fuer die Verbrauchsinformation.
Der EEPROM-Satz Motronik -404 + Getriebe -263 fuer den E32 740i 12/92 fuer Deinen Kollegen Gerard ist unterwegs nach Metz in Frankreich, danke
|
|
|
Aktive Benutzer in diesem Thema: 1 (Registrierte Benutzer: 0, Gäste: 1)
|
|
Forumregeln
|
Es ist Ihnen nicht erlaubt, neue Themen zu verfassen.
Es ist Ihnen nicht erlaubt, auf Beiträge zu antworten.
Es ist Ihnen nicht erlaubt, Anhänge hochzuladen.
Es ist Ihnen nicht erlaubt, Ihre Beiträge zu bearbeiten.
HTML-Code ist aus.
|
|
|
|